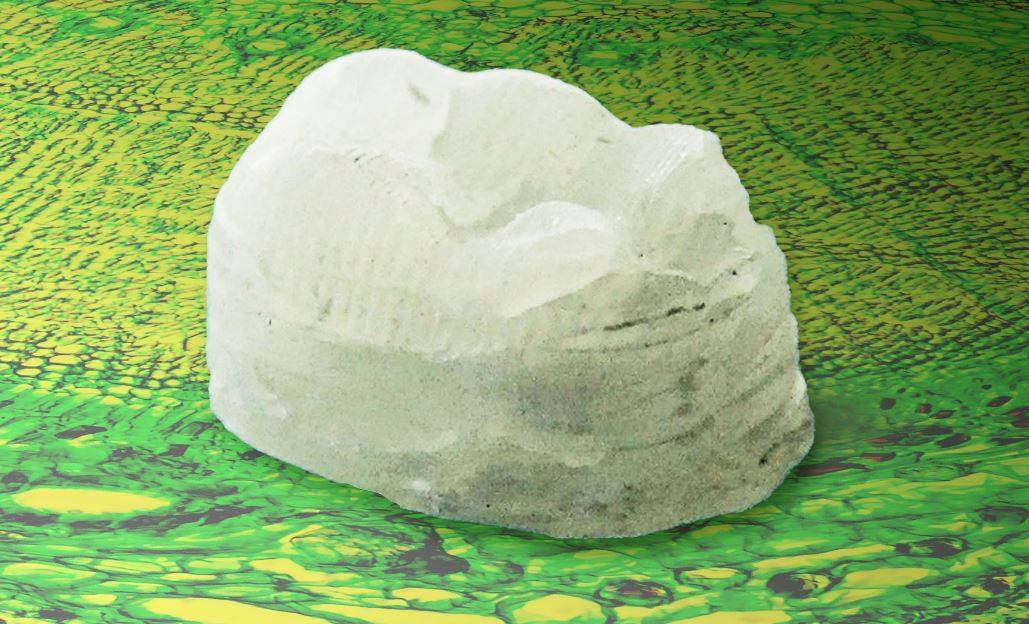
A single wood cell wall is made up of cellulose fibres, which are the most prevalent polymer in nature and the primary structural component of all plants and algae. Reinforcing cellulose nanocrystals, or CNCs, are chains of organic polymers organized in nearly perfect crystal patterns within each fibre.
CNCs are stronger and stiffer than Kevlar at the nanoscale. CNCs could offer a path to stronger, more sustainable, organically produced plastics if the crystals could be worked into materials in large fractions.
Cellulose-based Composite
An MIT team has developed a composite consisting primarily of cellulose nanocrystals with a small amount of synthetic polymer. The organic crystals make up 60 to 90% of the material, which is the largest percentage of CNCs yet obtained in a composite.
The cellulose-based composite was found to be stronger and tougher than some types of bone, as well as harder than ordinary aluminium alloys, according to the researchers. The material features a brick-and-mortar microstructure that resembles a mollusk nacre, which is the hard inner shell lining.
The team came up with a recipe for a CNC-based composite that they could make with 3D printing and traditional casting. They used penny-sized bits of film to evaluate the material's strength and hardness after printing and casting the composite. They also shaped the composite into the shape of a tooth to demonstrate how it may be used to create stronger, tougher, and more sustainable cellulose-based dental implants- or, for that matter, any plastic product- in the future.
"We can provide polymer-based materials mechanical capabilities they never have before by producing composites with CNCs at high loading," says A. John Hart, professor of mechanical engineering. "It's potentially better for the earth as well if we can replace some petroleum-based plastic with naturally derived cellulose."
Hart and his colleagues included Abhinav Rao Ph.D. '18, Thibaut Divoux, and Crystal Owens SM '17 published their findings in Cellulose today.
Gel Glues
More than 10 billion tonnes of cellulose are generated each year from plant bark, wood, and leaves. The majority of this cellulose is used to make paper and textiles, with a small amount being powdered for use in food thickeners and cosmetics.
cellulose nanocrystals, which may be isolated from cellulose fibres via acid hydrolysis, have been studied by scientists in recent years. Natural reinforcements in polymer-based materials could be made from incredibly strong crystals. However, due to the crystals' tendency to agglomerate and only weakly bind with polymer molecules, researchers have only been able to incorporate small fractions of CNCs.
Hart and his colleagues wanted to create a composite that had a high percentage of CNCs and could be shaped into robust, long-lasting forms. They began by combining a synthetic polymer solution with commercially available CNC powder. The team calculated the right amount of CNC and polymer to transform the solution into a gel that could be placed into a mould to be cast or fed through the nozzle of a 3D printer. They broke up any clumps of cellulose in the gel with an ultrasonic probe, making it more probable for the scattered cellulose to form strong links with polymer molecules.
They used a 3D printer to produce some of the gel and poured the rest into a mould to be cast. The printed samples were then allowed to dry. The material reduced during the procedure, leaving behind a solid composite made mostly of cellulose nanocrystals.
Rao explains, "We simply disassembled wood and reassembled it." "We reassembled the best components of wood, which are cellulose nanocrystals, to create a new composite material."
Tough Cracks
When the researchers looked at the structure of the composite under a microscope, they noticed that the cellulose grains settled into a brick-and-mortar pattern, similar to the architecture of the nacre. This zig-zagging microstructure in the nacre prevents a crack from traveling straight through it. This was also the case with the novel cellulose composite discovered by the researchers.
They used instruments to create nano- and micro-scale cracks to assess the material's resistance to cracks. They discovered that the arrangement of cellulose grains in the composite prevented cracks from breaking the material at numerous scales. The composite's hardness and stiffness are at the border between normal plastics and metals due to its resistance to plastic deformation.
The team is working on strategies to reduce gel shrinkage as they dry in the future. When printing little objects, shrinkage isn't an issue, but anything larger could buckle or shatter when the composite dries.
"You could keep scaling up, maybe to the metre size," Rao says, if you could avoid shrinking. "Then, if we dream big enough, we could use cellulose composites to replace a major portion of plastics."
(Source: Massachusetts Institute of Technology)