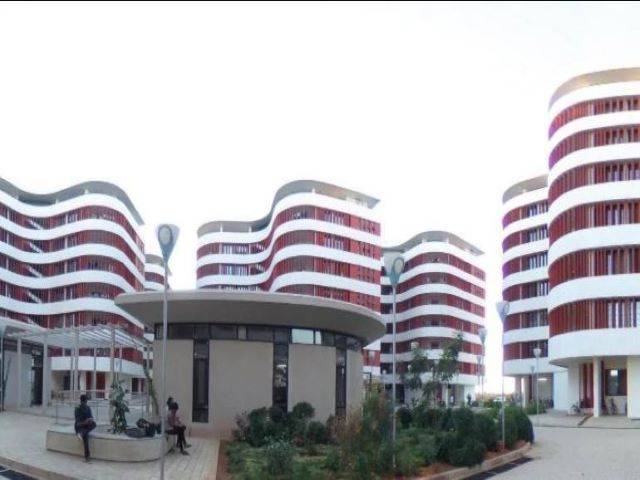
The taste of a dish changes with the addition of sugar or salt. Now these two important kitchen ingredients will be used to develop the nanocarbon catalyst to help in the production of Biofuel precursors at IIT Hyderabad.
Biofuels are typically derived from plant waste in many steps. They can, for example, be produced by the reaction between two chemicals, furfural and 2-methylfuran, both of which are derived from corncob. The reaction requires special enablers or catalysts, such as activated carbon, which in turn require heat treatment of the precursors to over 1,000° Celsius.
The catalyst shows better efficiency and selectivity than the commercially available variants to produce the desired C15 oxygenated hydrocarbon — a precursor to diesel and jet fuel.
The catalyst can be used to convert corncob wastes into valuable fuels. The researchers said that, currently, large quantities of this waste are being burnt due to lack of appropriate technology and awareness. The research was led by Atul Suresh Deshpande of the Material Science and Metallurgical Engineering and Sunil Kumar Maity of the Chemical Engineering Department with support from research students D Damodar, K Alekhya and V Mohan. Their work was published in the journal ACS Sustainable Chemistry and Engineering.
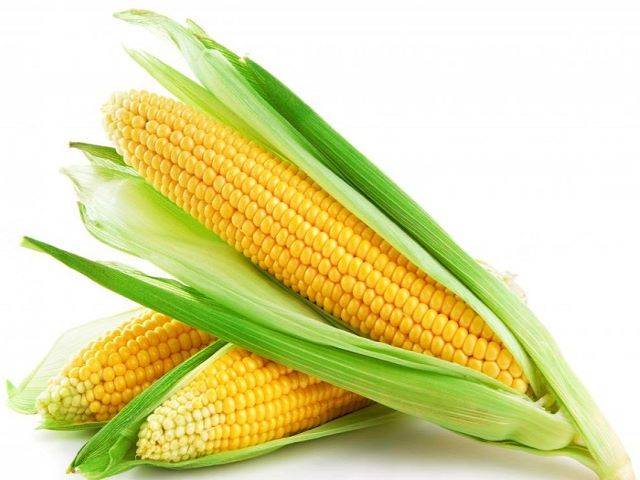
Uttar Pradesh, Andhra Pradesh and Telangana — the largest producers of corn — are expected to benefit in a big way. This would lead to additional earnings opportunities for farmers, providing sustainable energy source and reduction of carbon footprint in the automobile/aviation sectors. The need for such high energy not only increases the cost of the catalyst but also negates the attempts to carbon-neutrality in developing the biofuel. The researchers at IIT-Hyderabad have produced carbon catalysts at room temperatures using simple materials — sugar, sulphuric acid and salt.
“The dehydration of sugar by concentrated sulphuric acid is high-school chemistry. This reaction is exothermic — which means that intense heat is released during the reaction spontaneously, which helps in turning sugar into carbon without external heating,” said Deshpande.
“But this process is not well controlled and the resultant carbon does not have uniform micro-structure and catalytic prowess,” he added.
To control the microstructure of carbon during the process, the researchers added common salt. Salt
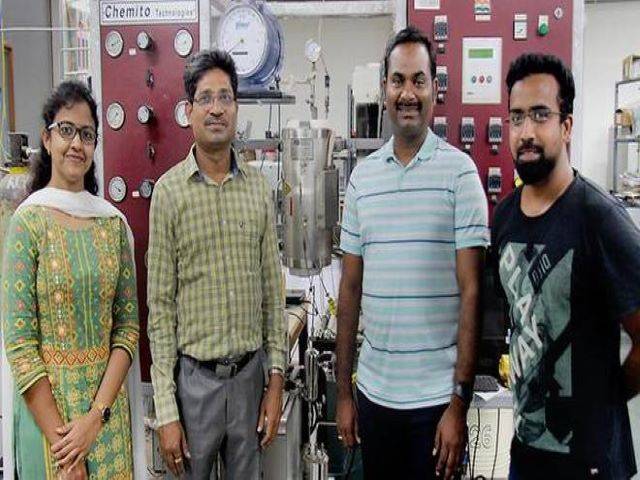
helps in controlled dehydration of sugar, which leads to the formation of carbon nanoplates — plate-like structures that are a thousand times smaller than human hair.
“This process of producing carbon nanoplates can be adapted for large-scale commercial production,” said Maity.
The researchers said that this approach can be modified to obtain not just carbon nanoplates but also other types of nano-structured carbon materials that are useful in other commercial applications. The use of biofuels instead of fossil fuels, is one of the most practical solutions towards achieving this goal.
The global aviation sector, which will account for 3.5 percent of carbon dioxide emissions and 15 percent of global oil demand by 2030, has resolved to halve reduction in carbon emissions by 2050.